Choosing Between Pneumatic and Electric Actuators: Key Differences, Advantages & Applications
05.27.2025 |
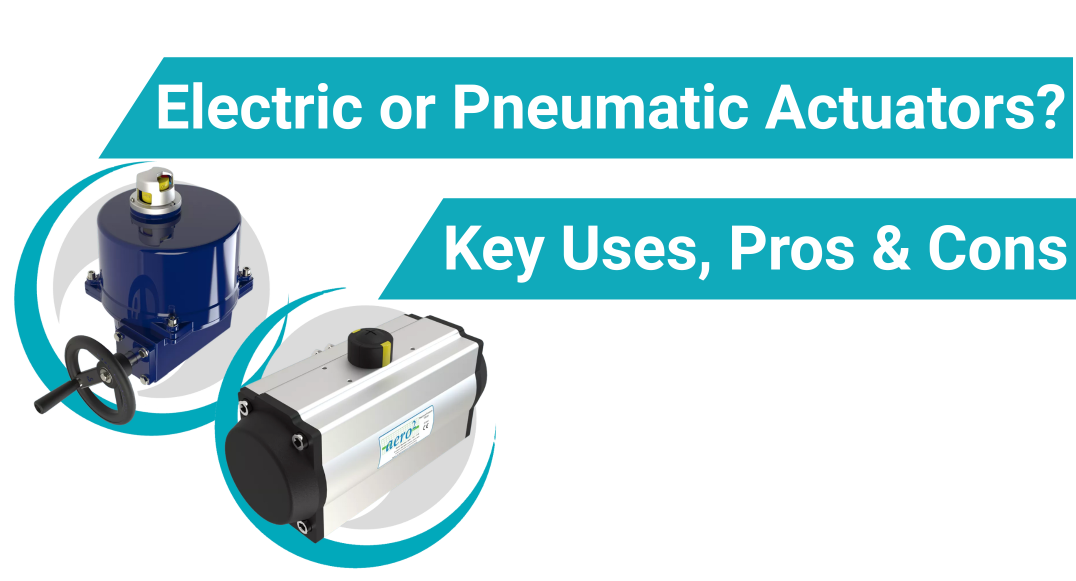
Overview
- Understanding Actuators in Valve Automation
- Pneumatic Actuators
- Electric Actuators
- Comparison Table
- Final Thoughts
Understanding Actuators in Valve Automation
Actuators are at the heart of valve automation, transforming energy into motion to position valves for flow control. Whether driving a simple on/off operation or a finely tuned modulating process, actuators play a critical role in system performance. The two predominant technologies—pneumatic and electric actuators—each bring distinct advantages depending on application requirements such as speed, precision, environmental conditions, and infrastructure.
Rather than a one-size-fits-all solution, choosing between pneumatic and electric actuators is about aligning their strengths with your operational goals.
Pneumatic Actuators: Speed and Safety in Harsh Environments
Pneumatic actuators are favored in applications where fast, reliable motion is essential and safety in hazardous environments is a priority. They excel in high-cycle operations and are especially well-suited for areas where explosive atmospheres restrict electrical components.
Why Choose Pneumatics:
- Rapid actuation: Ideal for fast-acting valves, with quick open/close times.
- Intrinsic safety: Operates without electrical components—perfect for hazardous or explosive zones.
- Compact power: Delivers high torque in a small footprint.
- Cost-effective startup: Lower initial investment when air infrastructure is already present.
Considerations:
- Requires a well-maintained compressed air system.
- Positioning precision may need external feedback systems.
- Air treatment (filters, dryers) adds ongoing maintenance needs.
Electric Actuators: Precision and Intelligence for Modern Control
Electric actuators provide accurate, programmable control with quiet, clean operation—making them a top choice in settings where precision, automation, and digital integration are vital. They shine in applications requiring tight modulation or integration into smart control networks.
Why Choose Electrics:
- Exceptional accuracy: Precise positioning and repeatability for demanding control tasks.
- Plug-and-play intelligence: Seamless integration with SCADA, PLCs, and IoT platforms.
- Low maintenance: No need for air lines or compressors—ideal for remote or indoor installations.
- Quiet, clean operation: No exhaust air or pneumatic noise.
Considerations:
- Higher upfront cost, though often offset by reduced maintenance and energy use.
- Electrical components require proper protection in hazardous areas.
- May lag in ultra-fast shutdown scenarios compared to pneumatics.
Pneumatic vs. Electric: Quick Comparison
Factor | Pneumatic Actuator | Electric Actuator |
---|---|---|
Power Source | Compressed Air | Electricity |
Response Speed | Very Fast | Moderate |
Precision | Moderate (requires feedback) | High |
Environmental Suitability | Ideal for hazardous/explosive areas | Requires electrical protection in hazardous areas |
Noise Level | Moderate (air exhaust) | Low (silent operation) |
Startup Cost | Lower (if air supply exists) | Higher |
Maintenance | Ongoing (air treatment) | Minimal |
Final Thoughts: Matching the Technology to the Task
Both pneumatic and electric actuators offer compelling capabilities. Pneumatics lead in speed, simplicity, and hazardous area performance, while electric actuators deliver superior control, integration, and cleanliness. The best choice depends on your application’s specific needs—often, a hybrid approach across a facility ensures the optimal balance of performance, safety, and efficiency.